Recognizing the Basics and Applications of Plastic Extrusion in Modern Manufacturing
In the world of contemporary manufacturing, the strategy of plastic extrusion plays an instrumental function - plastic extrusion. This complex process, entailing the melting and shaping of plastic via specialized dies, is leveraged across various industries for the production of varied items. From car components to durable goods product packaging, the applications are substantial, and the possibility for sustainability is similarly outstanding. Deciphering the fundamentals of this procedure reveals the true flexibility and potential of plastic extrusion.
The Basics of Plastic Extrusion Process
While it may show up complex, the basics of the plastic extrusion procedure are based on reasonably simple principles. It is a manufacturing procedure wherein plastic is thawed and after that shaped right into a constant account via a die. The raw plastic product, commonly in the kind of pellets, is fed right into an extruder. Inside the extruder, the plastic goes through heat and pressure, triggering it to melt. The molten plastic is after that forced with a shaped opening, known as a die, to form a long, continuous product. The extruded product is cooled and after that cut to the wanted length. The plastic extrusion process is thoroughly made use of in numerous sectors due to its adaptability, performance, and cost-effectiveness.
Different Types of Plastic Extrusion Techniques
Structure upon the basic understanding of the plastic extrusion process, it is needed to check out the numerous methods involved in this production method. In contrast, sheet extrusion produces big, flat sheets of plastic, which are commonly additional processed right into products such as food packaging, shower curtains, and cars and truck parts. Comprehending these methods is essential to making use of plastic extrusion successfully in modern-day manufacturing.

The Function of Plastic Extrusion in the Automotive Sector
An overwhelming majority of components in modern-day automobiles are products of the plastic extrusion process. This process has revolutionized the automotive market, transforming it into a much more efficient, cost-effective, and adaptable manufacturing market. Plastic extrusion is primarily used in the manufacturing of numerous auto elements such as bumpers, grills, door panels, and dashboard trim. The procedure gives an attire, consistent output, allowing manufacturers to create high-volume parts with great precision and marginal waste. The lightness of the extruded plastic components adds to the total reduction in vehicle weight, improving gas effectiveness. The longevity and resistance of these components click over here now to heat, cold, and effect boost the longevity of autos. Therefore, plastic extrusion plays a pivotal role in automobile production.
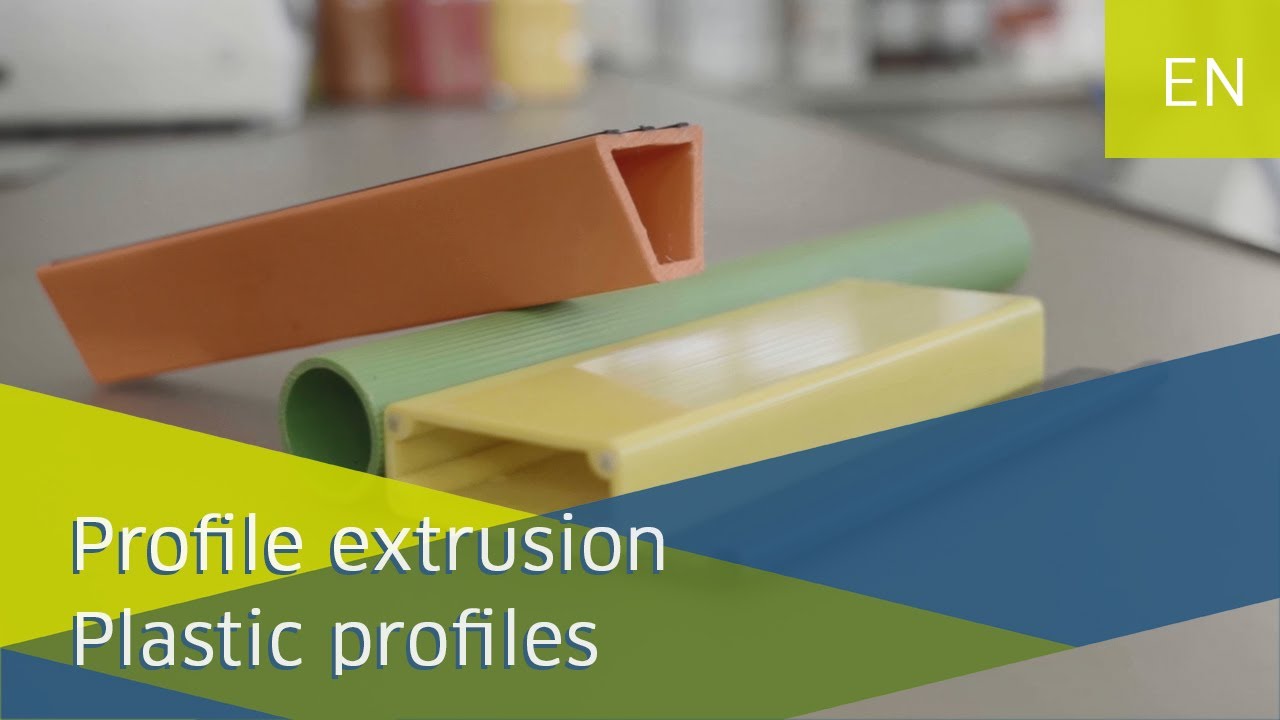
Applications of Plastic Extrusion in Customer Product Production
Beyond its considerable impact on the auto industry, plastic extrusion proves just as effective in the world of customer products manufacturing. The flexibility of plastic extrusion allows makers to design and generate complicated forms and sizes with high accuracy and performance. The adaptability, versatility, and cost-effectiveness of plastic extrusion make it a preferred choice for many customer items suppliers, contributing dramatically to the industry's growth and technology.
Environmental Effect and Sustainability in Plastic Extrusion
The prevalent use plastic extrusion in producing invites a fantastic read examination of its environmental effects. As a process that frequently utilizes non-biodegradable materials, the environmental influence can be substantial. Power usage, waste production, and carbon emissions are all concerns. Nonetheless, sector improvements are increasing sustainability. Effective equipment reduces power use, while waste monitoring systems recycle scrap plastic, lowering resources demands. Additionally, the development of naturally degradable plastics offers an extra eco-friendly choice. In spite of these improvements, further innovation is required to minimize the ecological impact of plastic extrusion. As society leans towards sustainability, makers should adjust to remain feasible, highlighting the value of constant study and innovation in this area.
Conclusion
In verdict, plastic extrusion plays a critical duty in modern-day production, specifically in the auto and customer goods sectors. Recognizing the basics of this procedure is key to enhancing its applications and benefits.
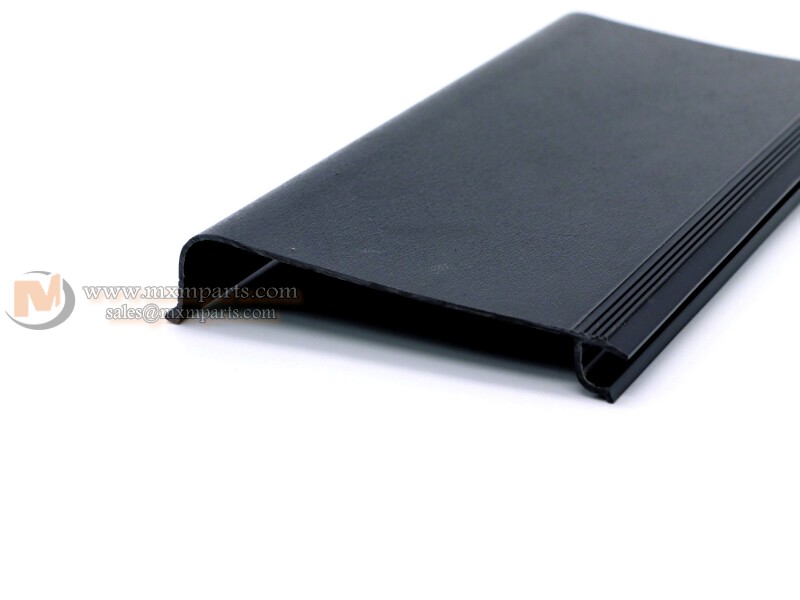
The plastic extrusion process is thoroughly made use of in various markets due to its cost-effectiveness, convenience, and efficiency.
Structure upon the basic understanding of the plastic extrusion process, it is needed to check out the various strategies involved in this manufacturing method. plastic extrusion. In comparison, sheet extrusion creates big, flat sheets of plastic, which are usually additional refined into products such as food product packaging, shower curtains, and automobile components.A frustrating majority go to website of parts in modern-day vehicles are products of the plastic extrusion process